Tr4 Tr5 double layer roll forming machine
Key words:
Product category:
Tel/Whatsapp:
Tr4 Tr5 double layer roll forming machine
RELATED MACHINES
TR4 AND TR5 DOUBLE LAYER ROLL FORMING MACHINE
Tr4 and Tr5 roofing sheets have gained significant popularity in the roofing and wall panel markets across South America, thanks to their impressive water-proof capabilities and appealing aesthetics. These sheets are not only functional but also enhance the visual appeal of various structures, making them a preferred choice for many builders and homeowners. Our advanced roofing sheet machine is designed to produce both Tr4 and Tr5 sheets, allowing for versatility in manufacturing. This machine boasts a remarkable forming speed that can reach between 8 to 15 meters per minute, ensuring efficiency in production without compromising quality. Additionally, the innovative double-layer machine design offers substantial benefits to our clients. By utilizing this design, clients can effectively save valuable workshop space, which is often a critical consideration in manufacturing environments. Furthermore, this design approach leads to significant cost savings in the purchasing process, as it eliminates the need for multiple machines dedicated to producing different types of sheets. Overall, our roofing sheet machine represents a smart investment for businesses looking to optimize their production capabilities while maintaining high standards of quality and aesthetics in their products.
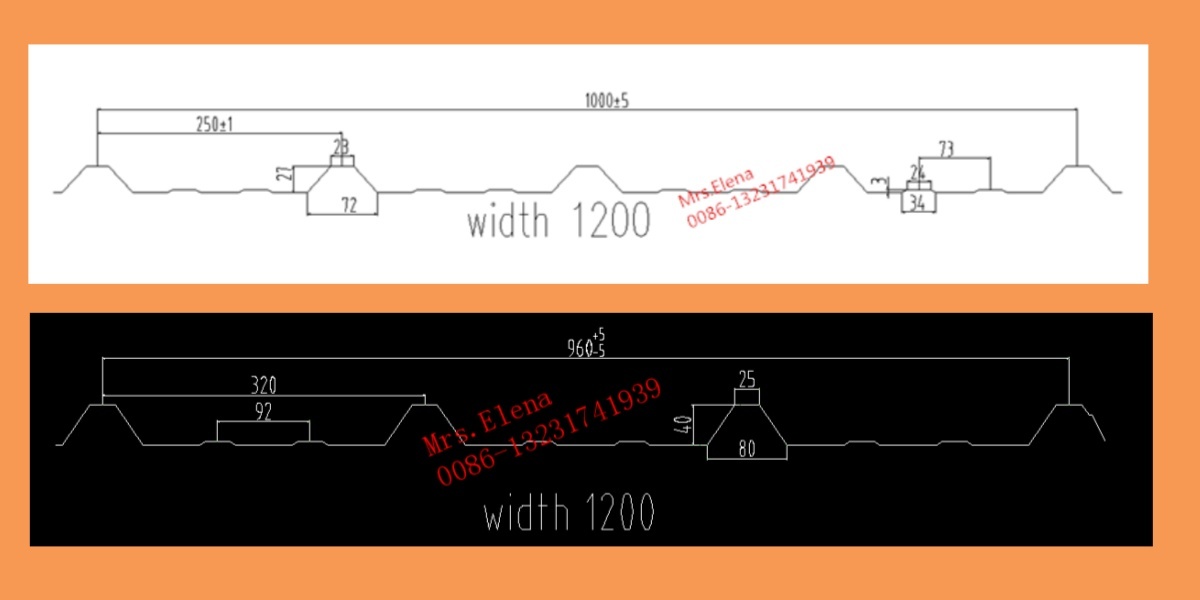
MACHINE COMPONENTS
NO. | Description | Quantity (set) |
1 | 5T hydraulic decoiler with coil car | 1 |
2 | Feeding Platform | 1 |
3 | Forming System | 1 |
4 | Transmission system | 1 |
5 | Hydraulic cutting system | 1 |
6 | Hydraulic pump station | 1 |
7 | Electric Control Cabinet | 1 |
8 | Automatic stacker | 6m |
9 | Spare parts and tools | 1 |
MACHINE PARAMETER
No | Item | Parameter |
1 | Raw material | PPGI |
2 | Thickness | 0.3-0.8 mm |
3 | Feeding width/coil width | 1200mm or 1220mm customized |
4 | Useful width | Tr4 960/1000 mm customized Tr5 1000 mm |
5 | Machine stands | iron plates welded |
6 | Forming Speed | 15 m/min - 40m/min customized |
7 | Forming station | Tr4 18 stations Tr5 15 stations |
8 | Total Power | 5.5 kw (main motor power) + 4 KW(hydraulic pump station motor power) |
9 | Mill bed material | 350H beams welded |
10 | Voltage | 380 V , 50HZ, 3 Phases |
11 | Diameter of shaft | 70mm diameter solid shafts |
12 | Cutting type | pillar guides |
13 | Forming Shaft | 45# steel with grinding process |
14 | Forming Roller | 45# steel with hard chrome coating process and overall quenching or customized Gcr15 bearing steel material |
15 | Cutting Blade | Cr12 with hard treatment |
16 | Transmission | 1 inch chain double row |
17 | PLC | DELTA Brands /MITSUBISHI |
18 | Touch Screen | DELTA Brand/MITSUBISHI |
19 | Electrical motor | SHANGHAI BOJIANG brand |
20 | Encoder | OMRON Brand with aluminum bracket |
21 | Low-voltage electrical | SCHNEIDER Brands |
22 | Host Machine rough size | L11m*W2m*H2.2m |
23 | Host Machine rough weight | 90000KGS |
24 | Machine with Anchor bolts | Have |
25 | Automatic Stacker | 6m long double deck |
MACHINE COMPONENTS DETAILS
1. DECOILER PART . THERE HAD HYDRAULIC / ELECTRIC/ MANUAL DECOILER CAN BE CHOOSE . MANUAL DECOILER WILL BE TOOK WITH MACHINE FREELY
7 Tons X 1250mm Wide Hydraulic Decoiler With Coil Car (customized )
2. PRE-CUTTER PART : THERE HAD HYDRAULIC / ELECTRIC/ MANUAL PRE-CUTTER CAN BE CHOSE
The PRE-CUTTER is an innovative tool designed to assist clients in significantly reducing their raw material wastage. By incorporating this advanced technology into your operations, you can achieve substantial savings on your material costs. If your purchasing budget allows for it, you have the option to select either a hydraulic or electric type of PRE-CUTTER. Both variants are equipped with the capability to pre-cut raw materials automatically when they reach your predetermined length in meters. This automation not only enhances efficiency but also ensures precision in cutting, thereby optimizing the use of your raw materials and minimizing excess waste. Investing in a PRE-CUTTER can lead to improved production processes and cost savings, making it a valuable addition to any manufacturing operation.
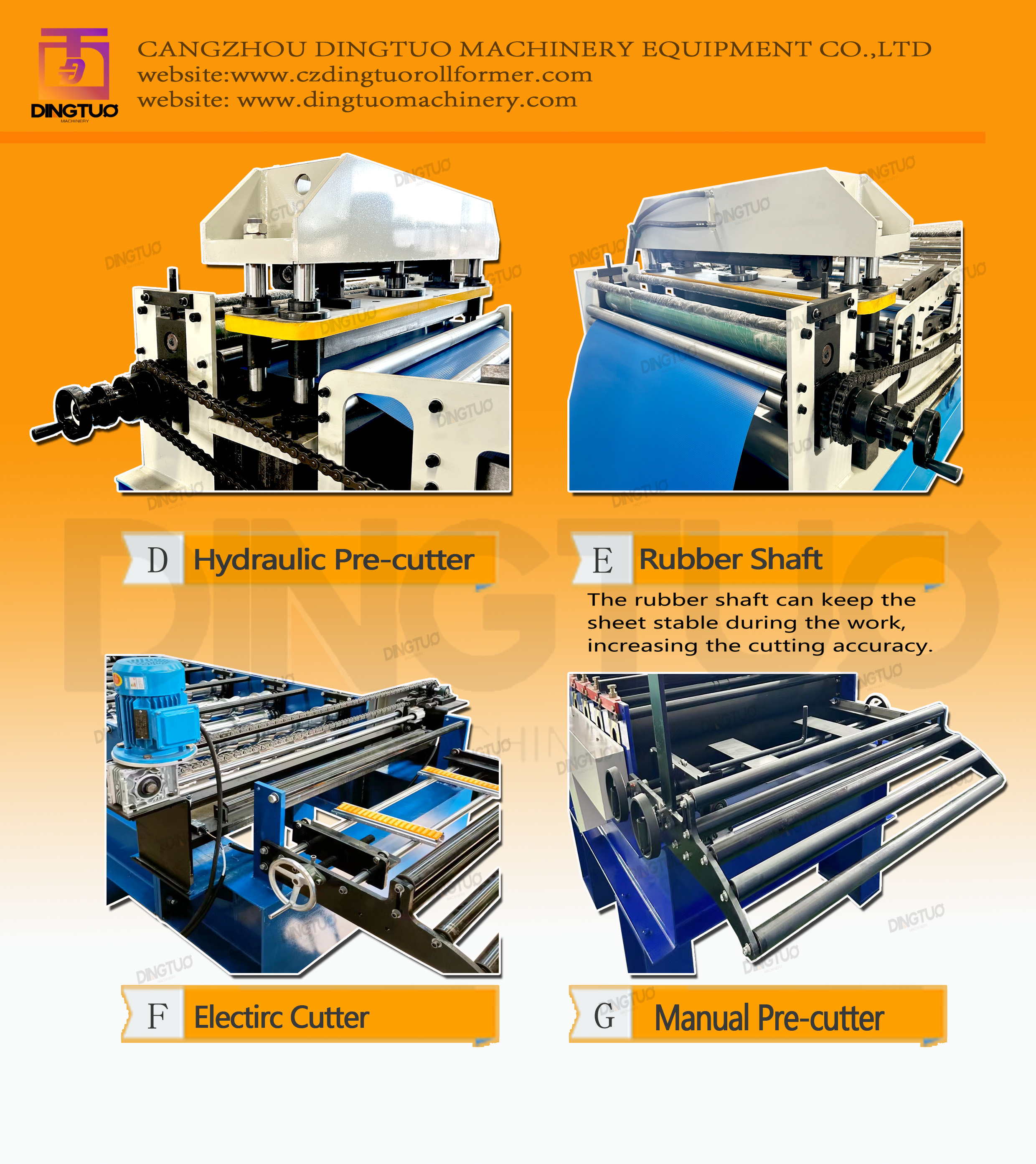
3. FORMING PART : THERE HAD H/I/J/K/L/M TYPE CAN BE CHOSE
The choice of the machine type is generally influenced by the speed at which it operates. For machines that run at a higher speed of 40 meters per minute, it is essential to select the H + J + L type. This selection is crucial because these types are designed with a more stable structure, which is necessary to handle the increased demands and potential vibrations that come with higher operational speeds. On the other hand, for machines that operate at a standard speed of 15 meters per minute, the I + K + M type can be utilized effectively. These types are suitable for moderate speeds and provide adequate performance without the need for the more robust features found in the H + J + L types. Therefore, the decision regarding which machine type to choose is closely tied to the operational speed, ensuring that the machine operates efficiently and reliably within its intended speed range.
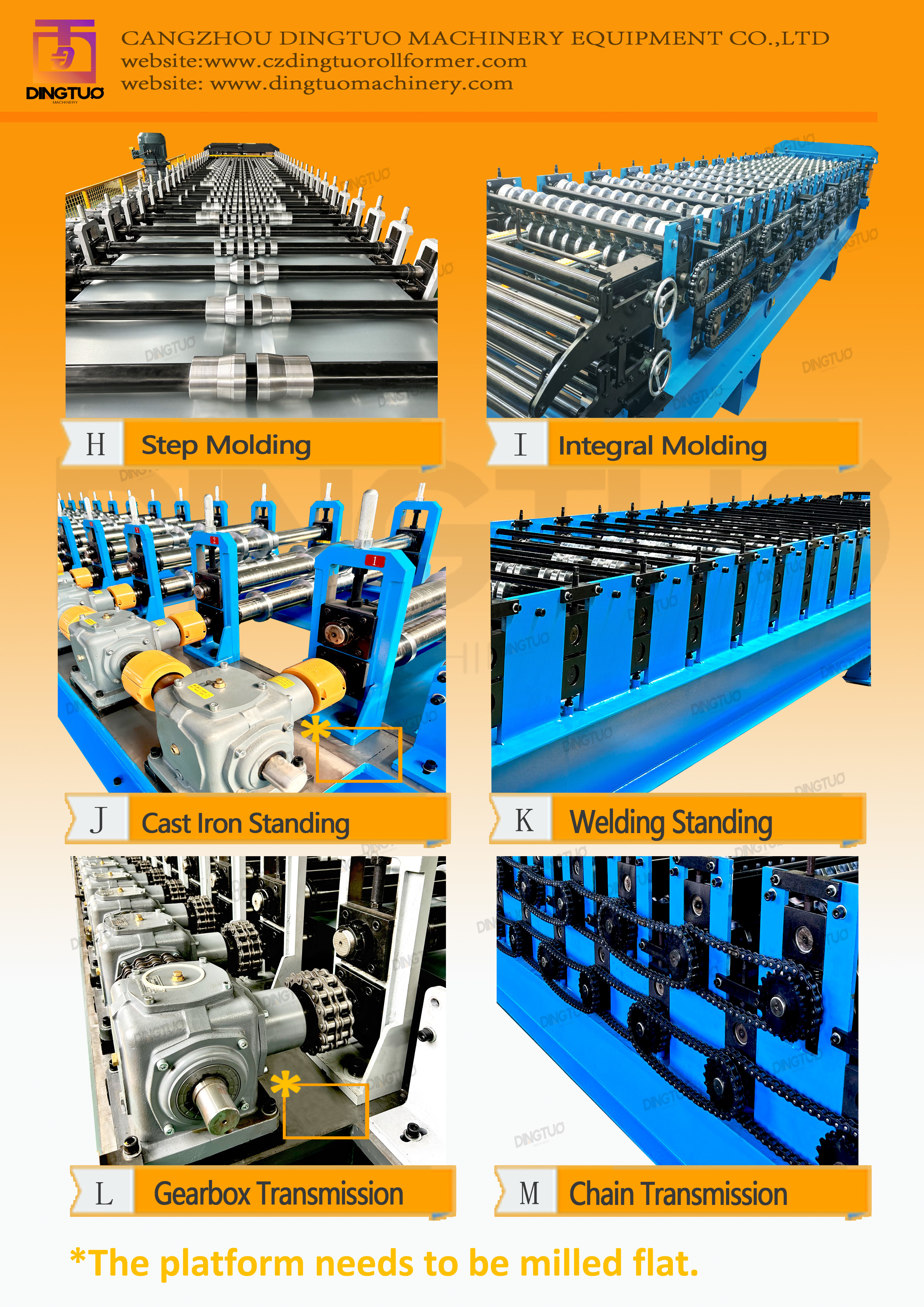
4. RECEIVING TABLE PART : THERE HAD STANDARD AND AUTOMATIC TYPE CAN BE CHOSE
The type of receiving system employed typically depends on the speed of the machine in operation. For instance, in cases where the machine operates at higher speeds, such as 25, 35, or even 40 meters per minute, the personnel may find it challenging to manually handle the sheets in a timely manner. At these elevated speeds, the staff simply does not have sufficient time to receive the sheets effectively without the risk of errors or accidents. Consequently, it becomes essential to implement an automatic stacker, which can efficiently manage the receiving of sheets without requiring constant human intervention. On the other hand, when dealing with standard machine speeds around 15 meters per minute, there is more flexibility in the receiving process. In these situations, operators can utilize a standard run-out table, which provides a designated area for the sheets to be placed after they are produced. Alternatively, if a run-out table is not available or necessary, the sheets can be allowed to drop directly onto the ground. This method, while less structured, can still be effective at lower speeds, allowing for a more straightforward and less labor-intensive process. Thus, the choice of receiving type is closely linked to the operational speed of the machine, influencing efficiency and safety in the workflow.
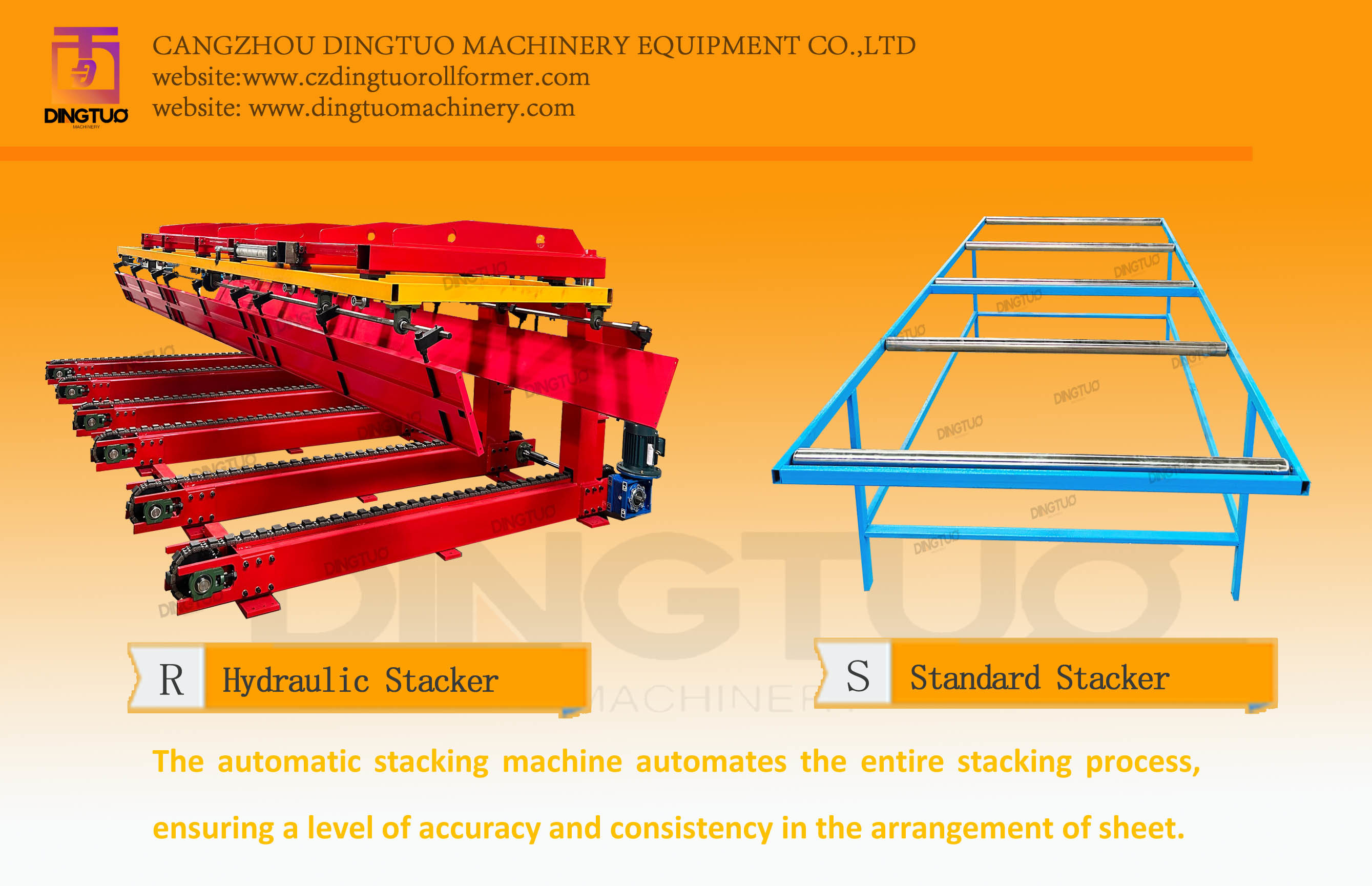
6m Double Layer Liftable Auto Stacker : speed fast and liftable stability (customized )

Spare Part
No. | Name | Quantity | Country |
1 | Rely | several | China |
2 | Encoder | 1pcs | China |
3 | Encoder wheels | 2pcs | China |
4 | bearings | 2pcs | China |
5 | Travelling Buttons | 2pcs | China |
6 | Switch buttons | 3pcs | China |
7 | The electromagnetic valve | 1pcs | China |
8 | Oil tubes | 2pcs | China |
9 | Gears | 2pcs | China |
10 | Chains | 2meters | China |
11 | circlip | Several | China |
12 | Tool Box | 1 Set | China |
Recommend Products
Product Consulting
Address: 50 Meters South Of China Petroleum Gas’
Tel/Whatsapp: +86 13231741939
E-mail: sales@czdingtuorollformer.com
E-mail: formingmachine55@gmail.com
Message consultation
WhatsApp / Wechat

